Manufacture of Cement
At the present time, Cement is one of the most important building materials.
When a strongly heated mixture of limestone and clay is mixed with a small amount of water, and this mixture allowed to set for a few hours, this mixture resembles a hard stone-like substance. After setting, the stone-like mass looks like as famous Portland rock of England, and hence it was named Portland cement.
Chemically cement is defined as the varying composition of a finely ground mixture of calcium aluminates and silicates, and this mixture is hydrated by mixing with water, therefore, form a rigid solid structure with good compressive strength.
Cement is a mixture of the following compounds:
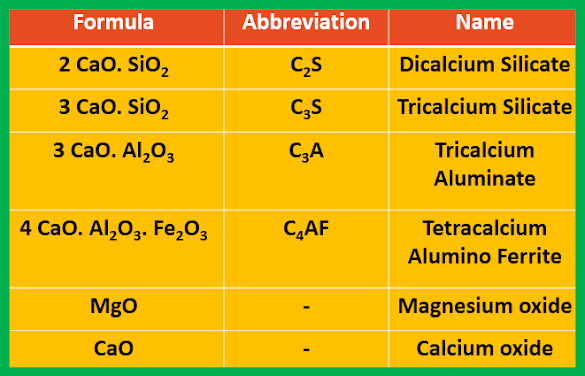 |
Composition of cement |
Average chemical composition of cement:
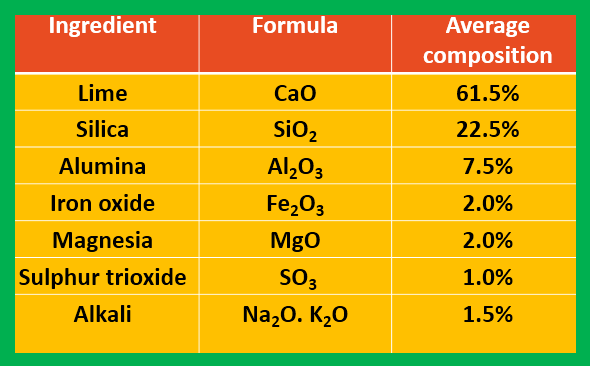 |
Average chemical composition of cement |
Raw Materials
The essentials raw materials for the manufacture of cement are limestone and clay which supply all the four principal ingredients, such as CaO, Al2O3, SiO2, and Fe2O3.
Calcium oxide and iron oxide, these both substance are obtained from limestone, while silica and alumina are obtained from the clay. Thus raw materials are two types---
1. Calcareous materials: limestone, calcium carbonate sludge, Marl, Chalk, and Alkali waste. These supply mainly CaO.
2. siliceous materials: Clay, Blast furnace slag, siliceous stone, Shale, Slate, etc. These supply silica, iron oxide, and alumina.
Cement making process
There are two methods of manufacturing cement.
1. Wet process.
2. Dry process.
The choice between two processes is usually governed by the following factors---
1. Physical conditions of raw materials.
2. Climate surrounding the place of manufacture.
3. Cost of fuel.
If limestone and clay are soft, the climate is fairly moist and the cost of fuel is cheap, the wet process is preferred.
In the wet process, the limestone is crushed in a suitable mill to prepared particles of suitable size, and clay is washed with water in a wash mill to remove flint and a slurry containing about 60% water is obtained. Crushed limestone and clay slurry are mixed in a special type of ball mill. The resulting slurry called raw slurry which further ground in tube mills and then stored in the collecting tanks, where after analysis addition is made to adjust the proportion. The raw slurry from the wet process is now introduced into the hopper provide on the upper part of a rotary kiln, which consists of an inclined steel cylinder which is about 200-300 ft long and 7-12 ft in diameter and the lower end provided with a fire hood, containing a short rotating cylinder. The charge moves forward slowly, due to the rotary motion (30-60 turns per hour) given to the kiln. The upper portion of the kiln is lined with ordinary brick, the middle portion is lined with thick fire brick and the lower firing zone is lined with fire clay bricks. A blast of burning coal dust and the air is blown from the lower end for a long time. The hot air obtained by cooling the hot clinker is also introduced into the kiln from the lower end. During its passage, the slurry first loses water in the upper portion and the remaining water is eliminated at about 7500C region when the charge centre in the middle portion of the kiln, the temperature rises to about 10000C. At this high temperature, limestone is decomposed into CaO and CO2. When the charge moves into the lowest portion, the hottest zone of the kiln, the temperature rises to about 14000C
to 16000C. At this temperature, the mixture is partly fused and the chemical reaction between CaO and aluminium silicate (clay) takes place resulting in the formation of calcium silicates and aluminates.
Reactions
CaCO3 ----> CaO + CO2
2CaO + SiO2 ---> 2CaO.SiO2 (Dicalcium
silicate)
3CaO + SiO2 ---> 3CaO.SiO2 (Tricalcium
silicate)
2CaO + Al2O3 ---> 2CaO.Al2O3
(Dicalcium aluminate)
3CaO + Al2O3 ---> 3CaO.Al2O3
(Tricalcium aluminate)
4CaO + Al2O3 + Fe2O3
---> 4CaO.Al2O3.Fe2O3
(Tetracalcium
alumino ferrite)
The resulting mass is either greenish-black coloured or grey coloured, and is called clinker. These are cooled in a rotary cooler and crushed. Generally, (2-3)% gypsum is added and finely ground to an exceedingly fine powder in grinding machines. The cement is filled in airtight bags to exclude moisture.
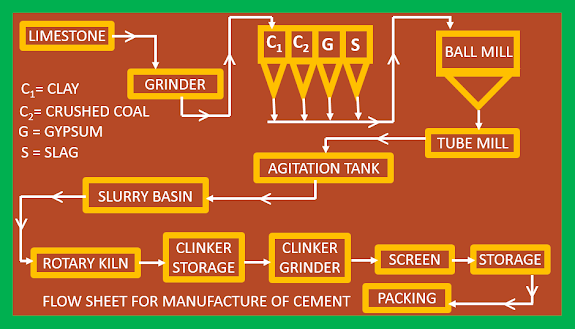 |
Flow sheet for manufacture of cement |